Durante los procesos de implantación de ERP en el sector de fabricación, encontramos muchas dudas acerca del número de operaciones óptimas a controlar. Por parte del cliente se pretende alcanzar un control exhaustivo de las distintas fases y operaciones, así que el trabajo del consultor ha de ser guiar y ayudar al cliente a determinar cuales son aquéllas imprescindibles o de misión crítica, cuales aconsejables y cuales accesorias. Un mayor número de fases y/o operaciones no implica un mayor control, sino que en ocasiones va en detrimento de la calidad de la información (normalmente debido a la incapacidad para poder controlarlas todas ellas), así como del trabajo añadido que suponen. Determinar el número óptimo de éstas es una de las labores críticas en la implementación del ERP. Lograrlo, desde mi punto de vista, constituye uno de los factores de éxito de la implantación.
Por poner un ejemplo en un sector con amplia experiencia, el de fabricación de mueble tapizado, con la implantación de un software ERP específico para tapicerías, DProduction.erp, observamos que algunas organizaciones requieren un control máximo de 5 o 6 procesos (corte, cosido, preparado, tapizado y embalaje), sin embargo otras, con una mayor cultura de la información, más capacidad de proceso de datos en planta y en definitiva mayor necesidad de control, pueden llegar hasta 20 o 25 fases.
Pensemos también que la infraestructura necesaria para llevar a cabo estos controles puede ser desde muy básica, hasta tremendamente compleja y/o cara. Las inversiones en planta, no en maquinaria productiva, pero sí en tecnología de la información (y por tanto no productiva a los ojos de muchos), suele ser difícil de entender por algunas organizaciones, así que hay que conocer las distintas alternativas de menor a mayor coste (en breve publicaremos con mayor profundidad sobre las distintas tecnologías):
- Códigos de barras. Tradicionalmente considerada de las tecnologías más baratas y de más fácil introducción en planta (quizá porque llevan más de 50 años entre nosotros) y por tanto los operarios de planta ofrecen menor resistencia a su introducción. Realmente no es una tecnología tan barata si los códigos se leen en planta, pues o bien requieren un PC (lectores conectados a PC), o bien son inalámbricos, en cuyo caso los precios son muy elevados.
- Identificación por Radio Frecuencia (RFID). Los chips y/o etiquetas RFID permiten almacenar información en éstos y su lectura no requiere un contacto directo como el código de barras. El uso de antenas permite la lectura/escritura de forma desatendida. Aunque puede usarse para todas las fases de fabricación, adquiere especial importancia en fases críticas de control como la carga y expedición de la mercancía. Hasta hace unos años era una tecnología prohibitiva en precio, hoy día maneja precios al alcance de cualquier organización.
- Dispositivos móviles (o fijos). El uso de ordenadores e incluso de tablets para el control de fabricación está alcanzando su punto álgido. Recibir el operario en su dispositivo las tareas que ha de realizar, ordenadas por prioridad, iniciar sus tareas indicándolo en el dispositivo, y cerrar éstas, permite un control con costes muy bajos y más intuitivos de lo que venían siendo hasta ahora. Además, no están limitados como las tecnologías anteriores, sino que permiten una mayor interacción entre el ERP y el operario.
En función de las necesidades y la cobertura que se pueda realizar en planta, podemos extender el número de procesos, sin embargo, debemos tener siempre a la vista que aquello que sea prescindible debe simplificar el modelo. Es decir, la hoja de ruta de fabricación debe tener un punto de partida simple, y con el tiempo, si es conveniente, ampliarla. Hacerlo al contrario maximiza el riesgo de «sobreinformación» sin aporte de valor alguno.
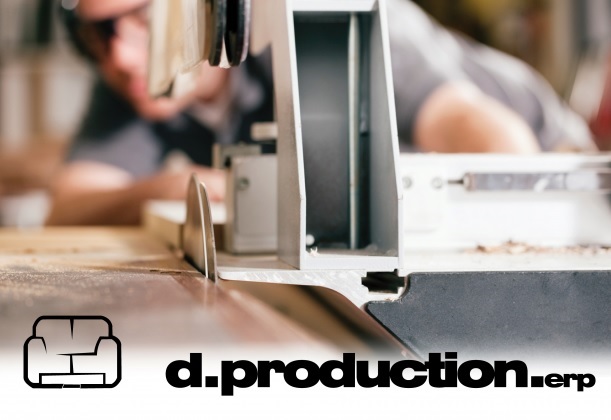
Software ERP específico para el sector del mueble tapizado / muebles / descanso
Así que, ¿de qué depende el número de procesos en un plan de producción?
Hay multitud de variables que afectan al número de procesos, y todas se basan en la necesidad de controlar lo que está pasando en el proceso. Pero principalmente hay que establecer un control en un proceso cuando:
- Queramos conocer el operario y/o máquina que realiza la operación, ya sea por temas de producción, productividad (incentivos, destajos, …), trazabilidad, etc.
- Provocar movimientos de almacén vinculados al proceso. Control de stock a tiempo real o prácticamente real.
- Control de situación de fabricación. Podremos conocer tiempo restante para finalizar la fabricación, para su expedición y entrega al cliente, para comprobar retrasos, etc.
- El coste del control es ínfimo en comparación del valor que reporta. Anécdota: Un amigo ingeniero industrial que trabaja para una gran empresa, dice que su técnica se basa en el «punto gordo». Como no dispongo de datos, mi nivel de precisión a adquirir equivale a no dar en el centro de la diana, sino en simplemente darle a la diana, como si fuese un punto muy gordo. Conforme voy adquiriendo información, mi objetivo se centra en reducir el tamaño de la diana a través de sus círculos concéntricos, pero nunca pretender que la diana se reduzca tanto como el punto central al que todos aspiramos acertar.
- Análisis de carga producción vs capacidad. Determinados procesos pueden representar cuellos de botella, por lo que analizar qué disponibilidad de tiempo tengo frente al ocupado, puede desencadenar decisiones tales como: horas extras, subcontratación, movimiento de recursos, etc.
Aunque habrá algunas más, éstas representan algunas de las cuestiones más importantes a valorar a la hora de modelar el plan de producción. Mientras no se requiera alguno de estos controles, el proceso debe ser simplificado en aras de la operativa y la reducción de transacciones sin valor.
Autor: Sergio Martínez
Recibe nuevos artículos mediante suscripción por e-mail, RSS o Feedly |
|
Un comentario
Pingback: ¿Debe el ERP permitirle trabajar con stocks negativos? Mundo.erp | Tecnologías ERP